How we’re engineering touch screens to eliminate ghost touch in mission-critical applications
We build many applications for customers that require absolute precision and reliability for environments where safety and accuracy are important.
We have been working with customers recently on engineering touch screens to absolutely eliminate any chance of ghost touch (false signals of touch inputs on a screen). This has required some creative thinking and deep-level engineering from our in-house display experts.
Examples of industries where high precision, safe touch screens are necessary include:
- HVAC control
- Hazard warning systems
- Industrial vehicle control
- Medical equipment
- Military applications
In these environments, we often design specific safety parameters to ensure reliable touchscreen performance. This includes:
- A redundancy host communication channel
- On-chip memory integrity checks
- Host communication integrity checks
- Power supply monitoring hardware
- PCAP (projective capacitative) validation
- FPC (flexible printed circuit) disconnect validation
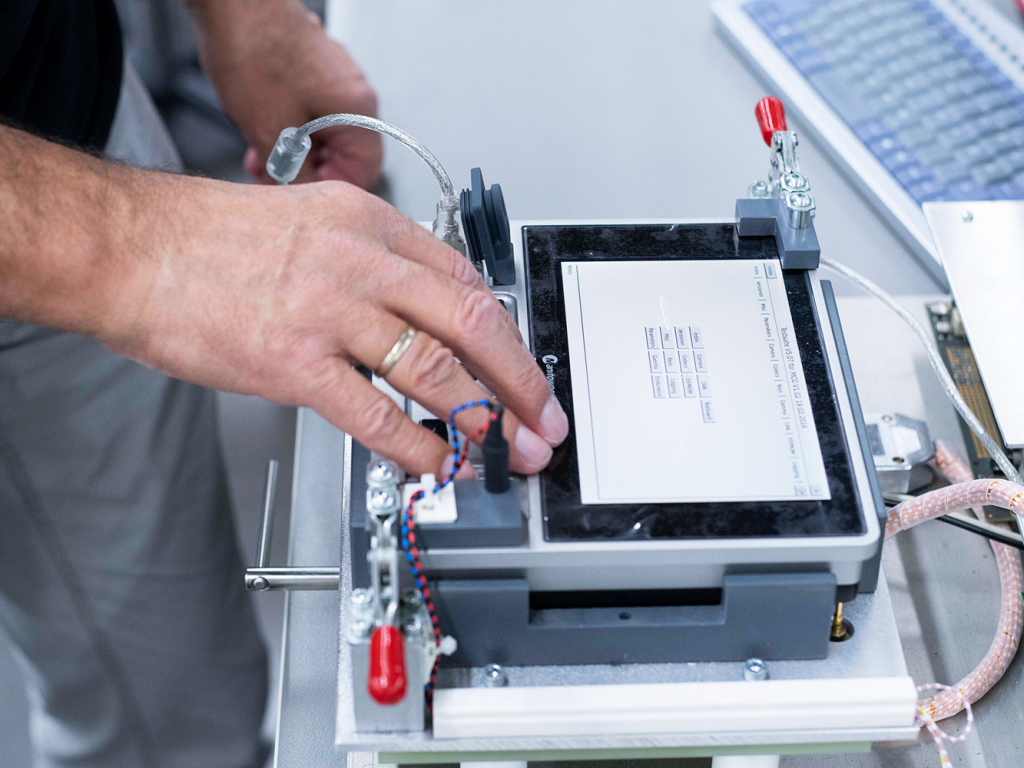
But even with all of these, false (ghost) touches can still be a problem.
One approach to recognizing if the touch is a real touch or a ghost touch, is to use another touch technology together with the PCAP sensor. For example, we can add an infrared bar alongside a PCAP.
The advantage with using two different sensor technologies is we can recognize with an extreme degree of accuracy if the touch is a real touch or a ghost touch, comparing the touch coordinates coming out from both systems.
The disadvantage is that the display requires a bezel for the IR emitters, and the solution is significantly more expensive.
We’ve taken a completely new approach.
Adopting a dual FPC (flexible printed circuit) with a master and slave design rule, adopting the latest generation of touch sensor driver ICs. By doing this, we have vastly reduced the potential for ghost touches while keeping costs down, and integration into your application optimized.